The yarn company Hobbii is Denmark's fastest-growing company. In a very short time, they have managed to create a huge business that is supported by modern technology and efficient work processes when handling the expected 1.5 million orders in 2021.
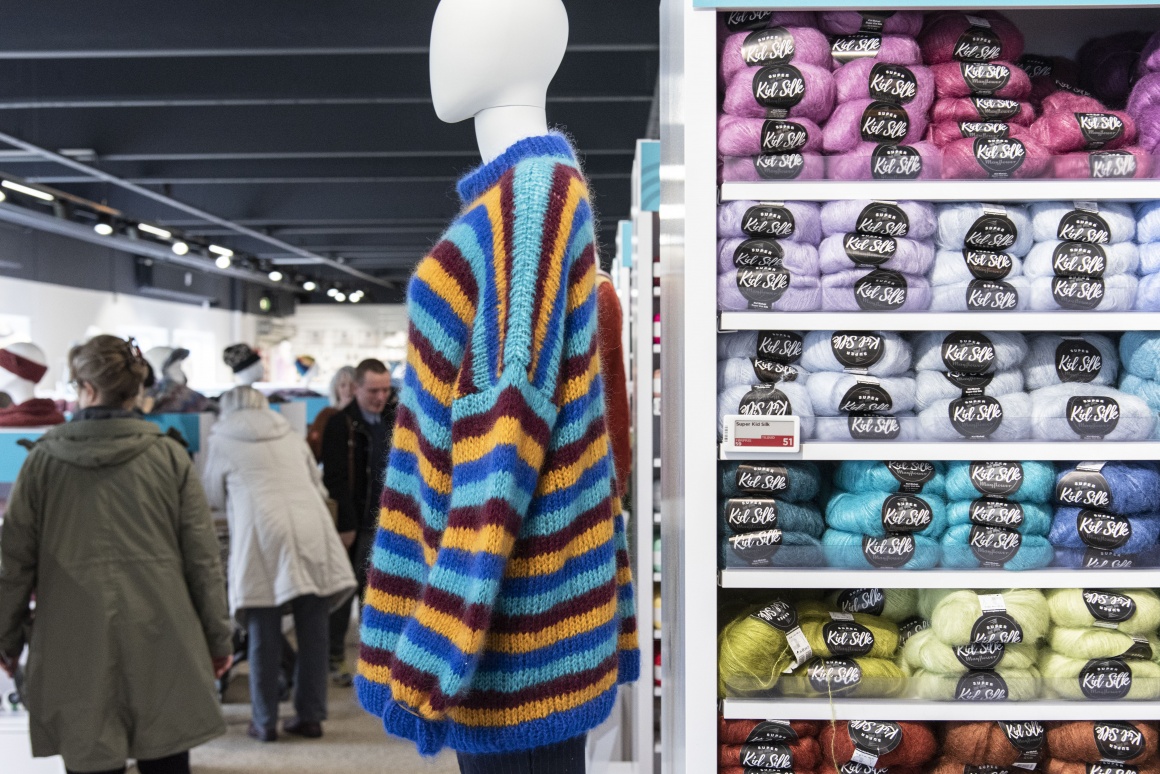
With 9,000 item numbers at their new giant warehouse in Greve (Denmark), there are many things to keep track of for the 250 staff members in the organization. This is one of the tasks that Delfi Technologies has helped Hobbii to solve. An integrated warehouse solution has been implemented to pick goods and efficient parcel handling via workstations in the warehouse. The solution includes several technologies, including touch screens, mobile phones, barcode scanners and label printers.
Started as an ecommerce business
Hobbii started its journey as a purely online store but has also begun to open more and more physical stores. Since Hobbii was born as a webshop, the company is hugely focused on data and processes with a focus on every detail in the transition from online to also establishing a physical business. Here, Hobbii has one goal - that customers should get the same good experience in a physical store as when they shop online. Using modern technologies from Delfi Technologies, Hobbii has succeeded in creating a close connection and synergy between the two sales channels.
"At Hobbii, we strive to always create the best customer experience. As we went from being a pure online player, to also having physical stores, we had to make sure there was a seamless experience between the two worlds. And that was the reason why we chose Delfi Technologies," says Jeppe Kallesøe, CEO at Hobbii. .
Physical stores with an online touch
Hobbii's stores are equipped with various IT solutions from Delfi Technologies, which give the customer an extraordinary experience. The prices in the store are always up-to-date with electronic price tags, which are linked to the webshop. It is both a resource-saving element, as the associates do not have to worry about changing prices, but also a service point to customers. Customers know for sure that they always get the same prices, whether they shop online or in stores.
Advanced price checkers are also placed among the yarn shelves and provide customers with additional information about the products, inspiration for knitting projects, and much more. The checkout area is an experience itself. A stylish area with elegant white POS systems and barcode scanners that complete the customer's last impression before leaving the store.
"In 2020, we won the Børsens Gazelle with a growth of more than 3,000 percent. When we choose a partner, we need someone who can help take us to the next level. That is why we chose Delfi Technologies ," says Jeppe Kallesøe
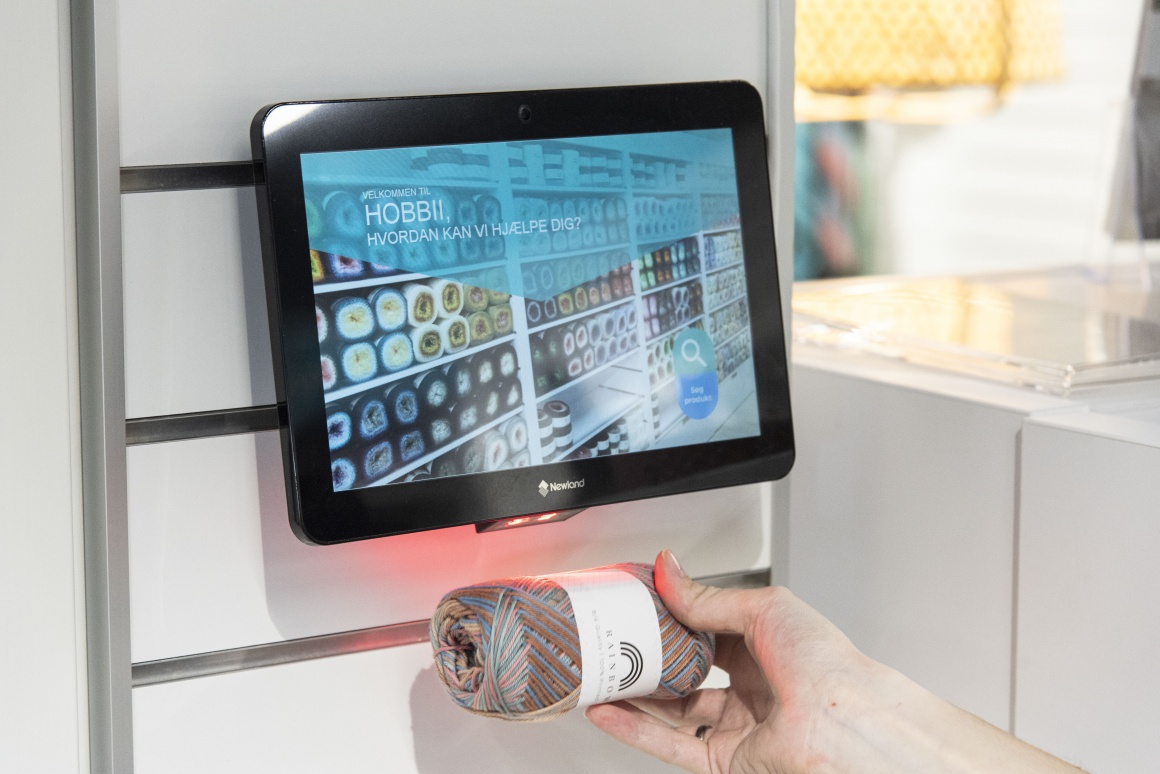
A scalable warehouse that can handle the enormous pressure
In the autumn of 2020, Hobbii moved their central warehouse to 10,000 m2 new storage facilities in Greve. On a good day, more than 10,000 packages are sent to customers worldwide. The most important task is that the customer must always receive their orders within 48 hours.
"With our number of packages, efficiency is everything for us in our warehouse. We have more than 9,000 item numbers and it therefore takes a lot to ensure that the right items arrive at the right customer, at the right time and the right price," explains Jeppe Kallesøe .
In order for this to be possible, the many warehouse workers work in day and night shifts. With so many different associates in the warehouse, it is a necessity to have stringent processes that are at the same time easy to understand, so that new associate easily can learn the routines.
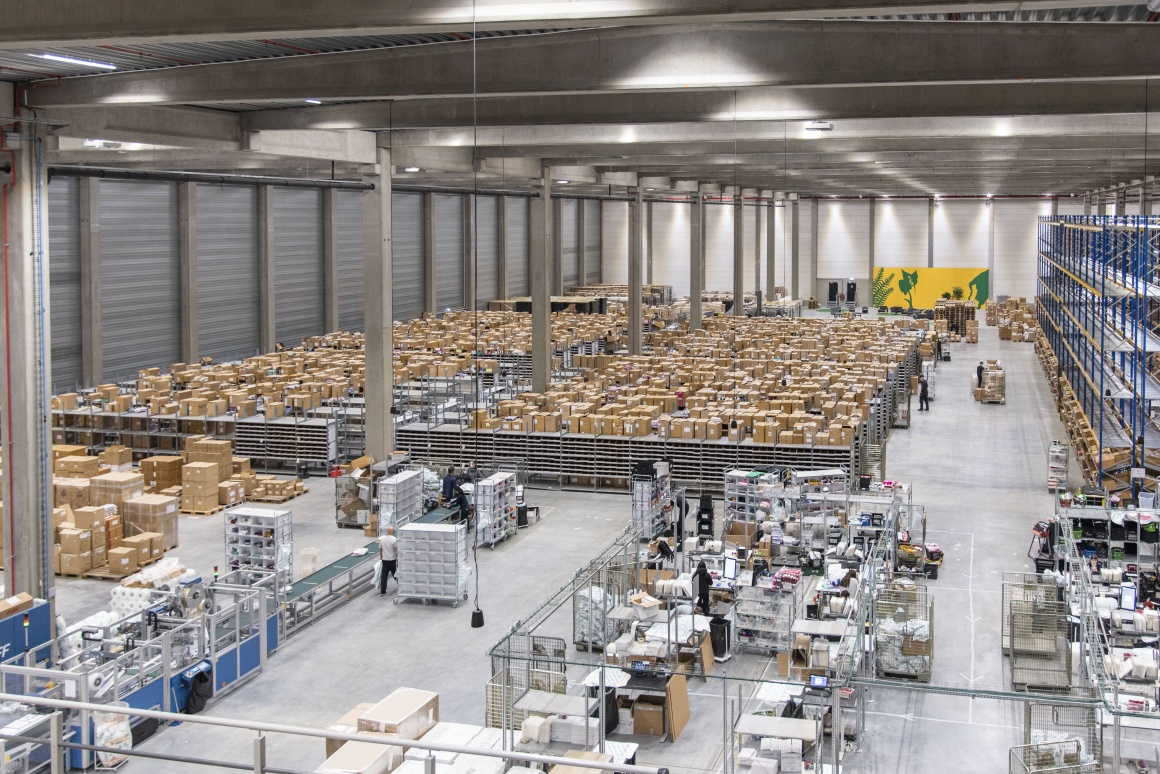
Faster picking with hands-free devices
Hobbii has chosen a solution where the associates in the warehouse use special gloves with an integrated barcode scanner. At the same time, a mobile phone is mounted on the arm with an overview of the order to be picked. Combining the solutions, the associates get a good working environment, as they have both hands free when the goods must be picked and packed. The picking order is also optimized based on the warehouse structure, so that the picking route is as short as possible, which streamlines the entire order handling.
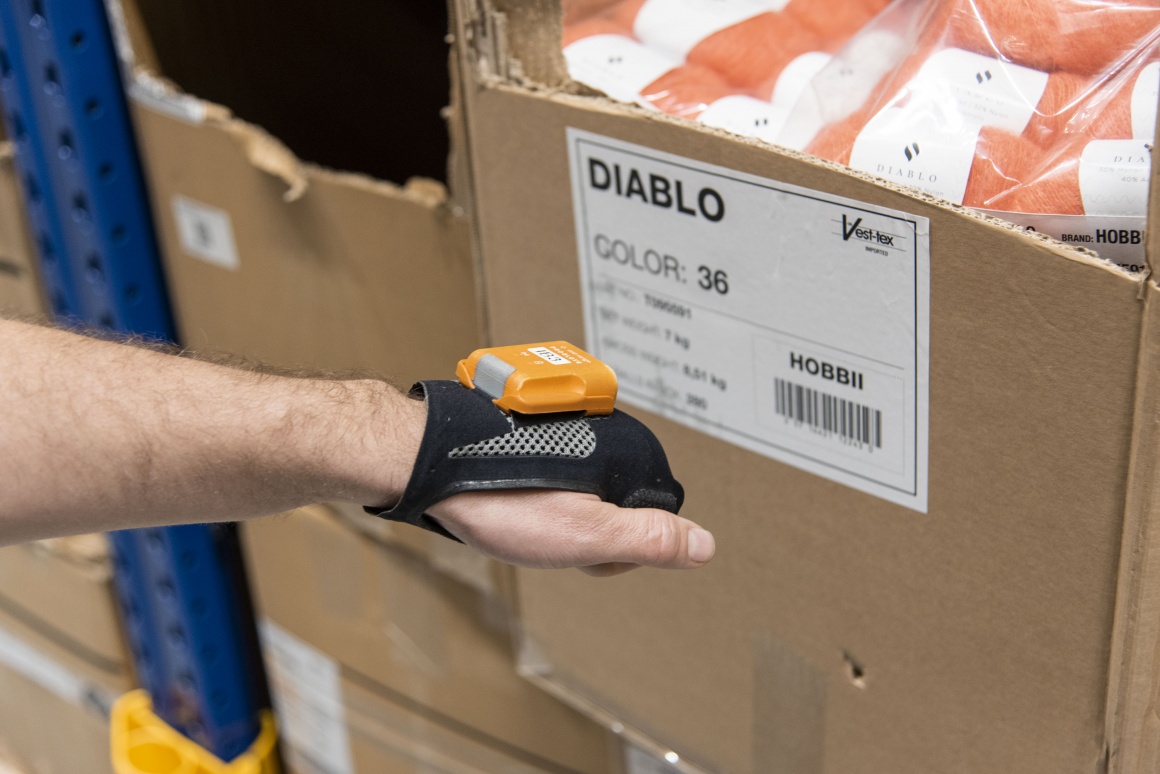
Packing stations make order packing like a game
Hobbii has 16 packing stations in the warehouse, and at each station the associate can get a quick overview of open orders via a touch screen, where they can see the entire order. From here, they can also print shipping labels and complete the orders. The solutions provide the ability to grow as they can scale up and down as needed, which is another advantage during busy periods like Black Friday when sales are booming.