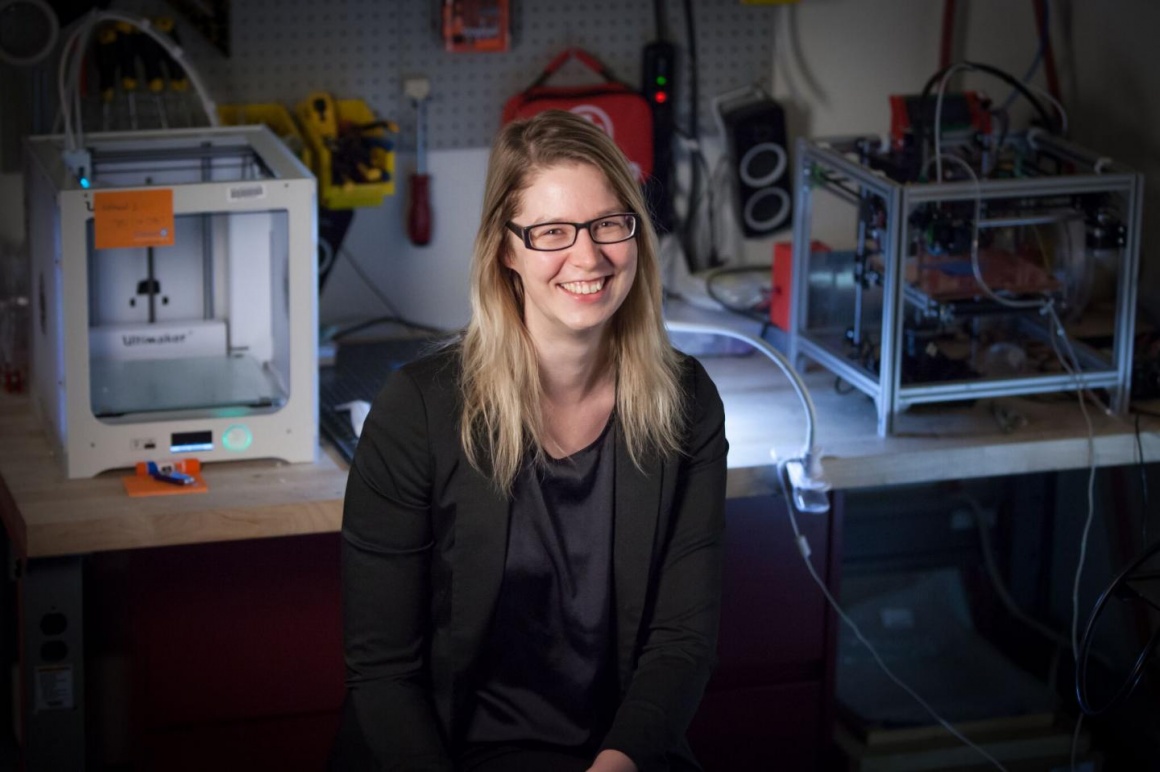
3-D printing has come a long way since the first "rapid prototyping" patent was rejected in 1980. We've evolved from basic designs to a wide range of highly-customizable objects. Still, there's a big issue: once objects are printed, they're final. If you need a change, you'll need a reprint.
But imagine if that weren't the case - if, for example, you could recolor your iPhone case or earrings to match whatever outfit you're wearing.
Researchers from MIT's Computer Science and Artificial Intelligence Laboratory (CSAIL) have gotten closer to making that a reality. In a new paper, they present "ColorFab", a method for repeatedly changing the colors of 3-D printed objects after fabrication.
Using their own 3-D printable ink that changes color when exposed to UV light, the team can recolor a multi-colored object in just over 20 minutes - and they say they expect that number to decrease significantly with future improvements.
While the project is currently focused on plastics and other common 3-D printing materials, the researchers say that eventually people could instantly change the color of their clothes or other items.
"Largely speaking, people are consuming a lot more now than twenty years ago, and they're creating a lot of waste," says MIT professor Stefanie Mueller, who co-wrote the new paper about the system. "By changing an object's color, you don't have to create a whole new object every time."
Mueller co-wrote the paper with postdoc Parinya Punpongsanon, undergraduate Xin Wen, and researcher David Kim. It was accepted to the ACM CHI Conference on Human Factors in Computing Systems, which takes place in April in Montreal.
How it works
Previous color-changing systems have been somewhat limited in their capabilities, such as single-colors and 2-D designs.
To move beyond single-color systems, the team developed a simple hardware/software workflow. First, using the ColorFab interface, users upload their 3-D model, pick their desired color patterns, and then print their fully colored object.
Changing the multi-colored objects involves using UV light to activate desired colors and visible light to deactivate others. Specifically, the team uses a UV light to change the pixels on an object from transparent to colored, and a regular office projector to turn them from colored to transparent.
Once a user has placed the object on the platform, they can select colors using the interface.
The team's custom ink is made of a base dye, a photo-initiator, and light-adaptable dyes. The light-adaptable or "photochromic" dyes bring out the color in the base dye, and the photo-initiator lets the base dye harden during 3-D printing.
The team tested ColorFab on three criteria: recoloring time, precision, and how quickly the color decayed. As far as timing, a full recoloring process took 23 minutes. However, the team notes that they could speed up the process by using a more powerful light or adding more light-adaptable dye to the ink.
The researchers also found the colors to be a bit grainy, which they hope to improve on by activating colors closer together on an object. For example, activating blue and red might show purple, while activating red and green would show yellow.
Mueller says that the goal is for people to be able to rapidly match their accessories to their outfits in an efficient, less wasteful way. Another idea is for retail stores to be able to customize products in real-time, like if a shopper wants to try on an article of clothing or accessory in a different color.
"This is the first 3-D printable photochromic system that has a complete printing and recoloring process that's relatively easy for users," says Punpongsanon. "It's a big step for 3-D-printing to be able to dynamically update the printed object after fabrication in a cost-effective manner."