Conventional packaging meets many demands – intelligent packaging can do even more. It is proactive and provides information about the condition, time and location of the transported goods. This is made possible by sensors applied on or inside the tertiary packaging. In this interview with iXtenso, Dr. Volker Lange, Head of Packaging and Retail Logistics at the Fraunhofer Institute for Material Flow and Logistics, delivers insights into the future of packaging logistics.
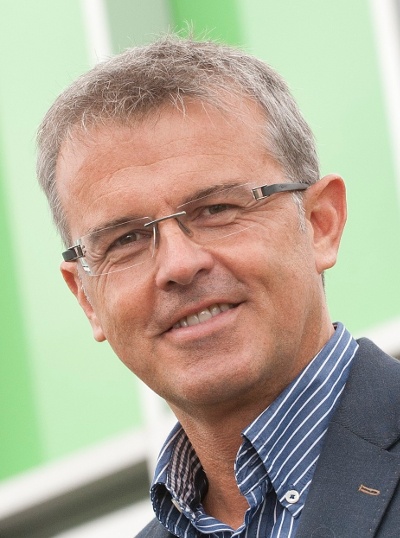
Dr. Lange, what is essential when it comes to packaging materials and containers to make them efficient and sustainable?
Packaging optimization in the retail sector includes packaging inserts und consumption. You ensure that overpacks are being avoided and eliminated for example. The reduction in packaging material use is a primary focus in this case. Another emphasis is on the use of modular packaging to optimally utilize the space, both on the pallets as well as ultimately on the shelves. The concept of reduction is consistent with ecologically worthwhile resource management.
Another element in the context of sustainability is packaging materials and packing supplies. There is currently a lot of research done into the area of biobased materials to study how other sustainable packaging materials can be brought into retail logistics. Having said that, this is not the focus of logistics but rather an emphasis of the packaging industry.
In actual logistics, it is essential for packaging to efficiently perform its task. That is to say that the products fit the packaging, while the packaging simultaneously fits the carriers, so they can be optimally transported, stored and turned over. The integration of packaging into the entire supply chain – that is the biggest challenge for logistics.
GS1 Germany has initiated a project designed to use cross-company and standardized reusable transport packaging for retail shipments. What are the advantages of a uniform system?
The use of returnable containers is meant to help reduce cardboard packaging as it pertains to repackaging and distributing of goods. Repackaging processes at central warehouses should be avoided whenever possible. Another advantage is the fact that uniform containers can be used by several partners, in this case by manufacturers and retailers. Thanks to the exchange, the total quantity of containers is being reduced. When reusable containers are used throughout the supply chain, individual steps in the process are being avoided.
An additional advantage of uniform and standardized reusable packaging is the optimal packing of pallets. Thanks to the increased stability and the modular containers, the pallets can be filled all the way to the top. This means the utilization is usually greater compared to disposable packaging. In this case, the heterogeneity in packaging limits both height and stability. According to the participants, the number of transported pallets was reduced during the project.
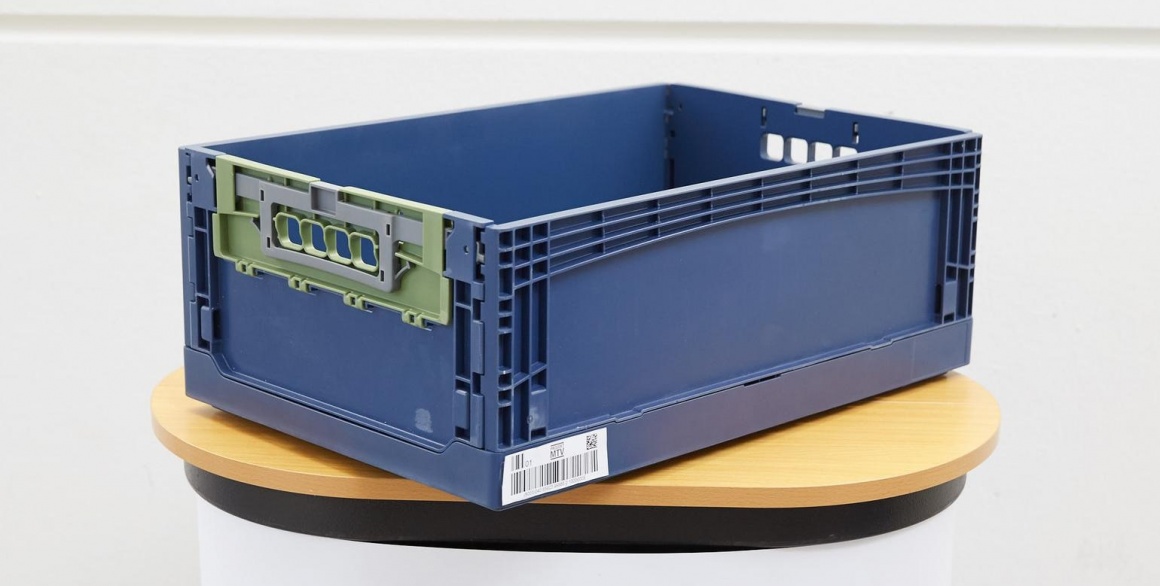
How does digital transformation presently help to optimize packaging logistics?
Digital transformation offers great potential for retail logistics. Data is the crucial factor in all this. For example, when it comes to improving planning methods: in this case, the emphasis is on “dimensioning“. That is to say, exact data of products, sales, and transport packaging enables logisticians to dimension the entire supply chain via intelligent software. In doing so, the rate of capacity utilization of carriers can be optimized for example. Transports are maximized, and warehouses better stocked, while the planning process is minimized at the same time. The overall logistics process can be considerably better controlled and managed.
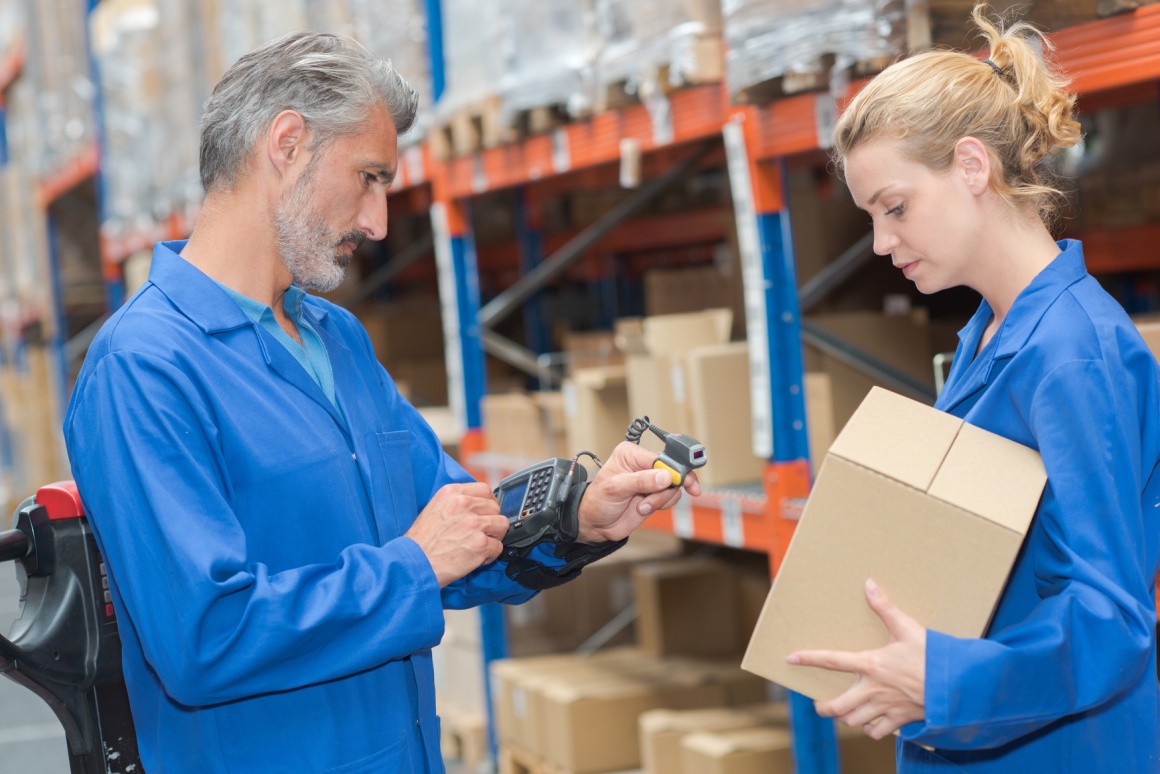
Which areas should be more digitized in the future?
The objective of digital transformation is to increase transparency and networking. Intelligent packaging is able to make a fundamental contribution in this case. Transport packaging subsequently no longer just fulfills the classic functions of protection, transport or storing but provides important information at the same time. Sensors collect data from the surroundings that describe the condition and state of goods. They detect where pressure was put on the packaging or determine the degree of vibration a packet encountered. Temperature patterns or humidity can also be measured to verify whether the cold chain remained unbroken and maintained. All these processes become even more efficient in the case of reusable packaging. Localization is another aspect that is expedited by digital transformation. After all, if the packaging is also equipped with Auto-ID and RFID solutions, it can provide information about its location and delivery routes.
What will packaging logistics look like in the year 2030?
My personal vision involves the clear distinction between the packaging and carriers. We call this serialization. It means that if you are able to distinguish individual pallets from one another, the amount of information increases as a result. In doing so, key performance indicators such as turnover rates, downtimes, damages, quality losses and shrinkage can be made transparent. Intelligent packaging and carriers subsequently play a crucial role in managing the entire supply chain in a more transparent, efficient and near real-time manner.