To maintain competitive advantage, logistics service providers and retailers have embraced automated order picking in their warehouses by implementing pick-to-cart, pick-to-light, voice picking and other technologies. However, despite the success of these ICT solutions, considerable benefits can also be achieved by reorganising key logistics processes.
How to implement a multi-order picking solution and how to avoid potential obstacles?
Identify the optimal order picking method
The optimal order picking method depends on many factors, such as the product range, peak period volumes, resource, warehouse size, number of customer orders and the desired delivery times. Without an analysis of these factors and identification of the key logistics bottlenecks, any investment in an automation solution will not yield optimal efficiency. It is also important to determine which underlying technology will provide the most benefits.
Distinguish between dynamic or static order picking
To find the best picking method, it is important to distinguish between dynamic and static order picking:
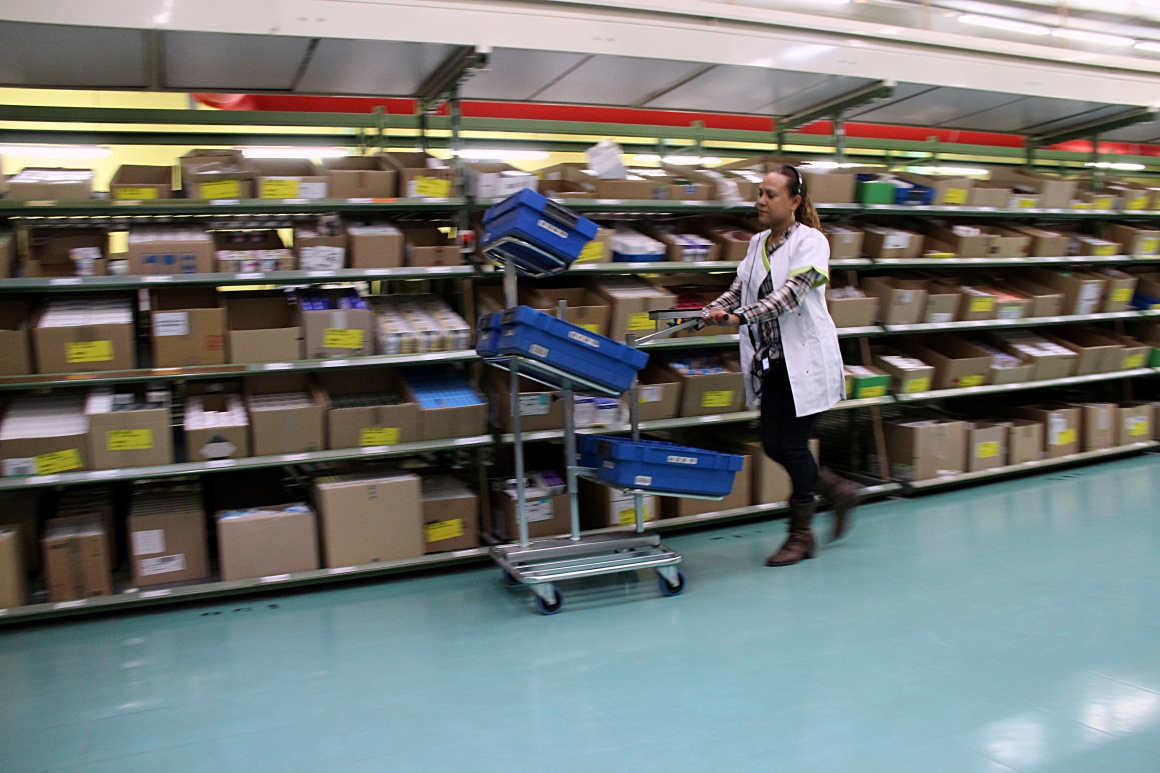
Dynamic order picking
The operators remain in a fixed location and all the ordered items are provided within their reach – for example, in a robotised warehouse. Dynamic order picking has the important advantage of eliminating all travel distances.
Static order picking
Each picker goes to the storage locations, either by foot or with a picking trolley or a forklift.
A further distinction with static order picking is between single- and multi-order picking. If most orders have many SKUs, the travel times between the items are often short and single-order picking is probably the best solution. However, if there are only a small number of items for each order, then multi-order picking can be a time saver.
Assess and minimise travel distances
The choice for single or multi-order picking can lead to considerable differences in efficiency. With multi-order picking, the primary goal is usually to minimise travel distances. This is done by picking all items for several orders (multi-order picking) on a single route, or by picking the total quantity of one specific SKU for several customers at the same time (batch picking).
With these two options, all picked items must also be assigned to the right customer orders in an intelligent manner. If splitting the items after picking takes too much time or leads to errors, the potential efficiency improvement drops, or the delivery reliability suffers.
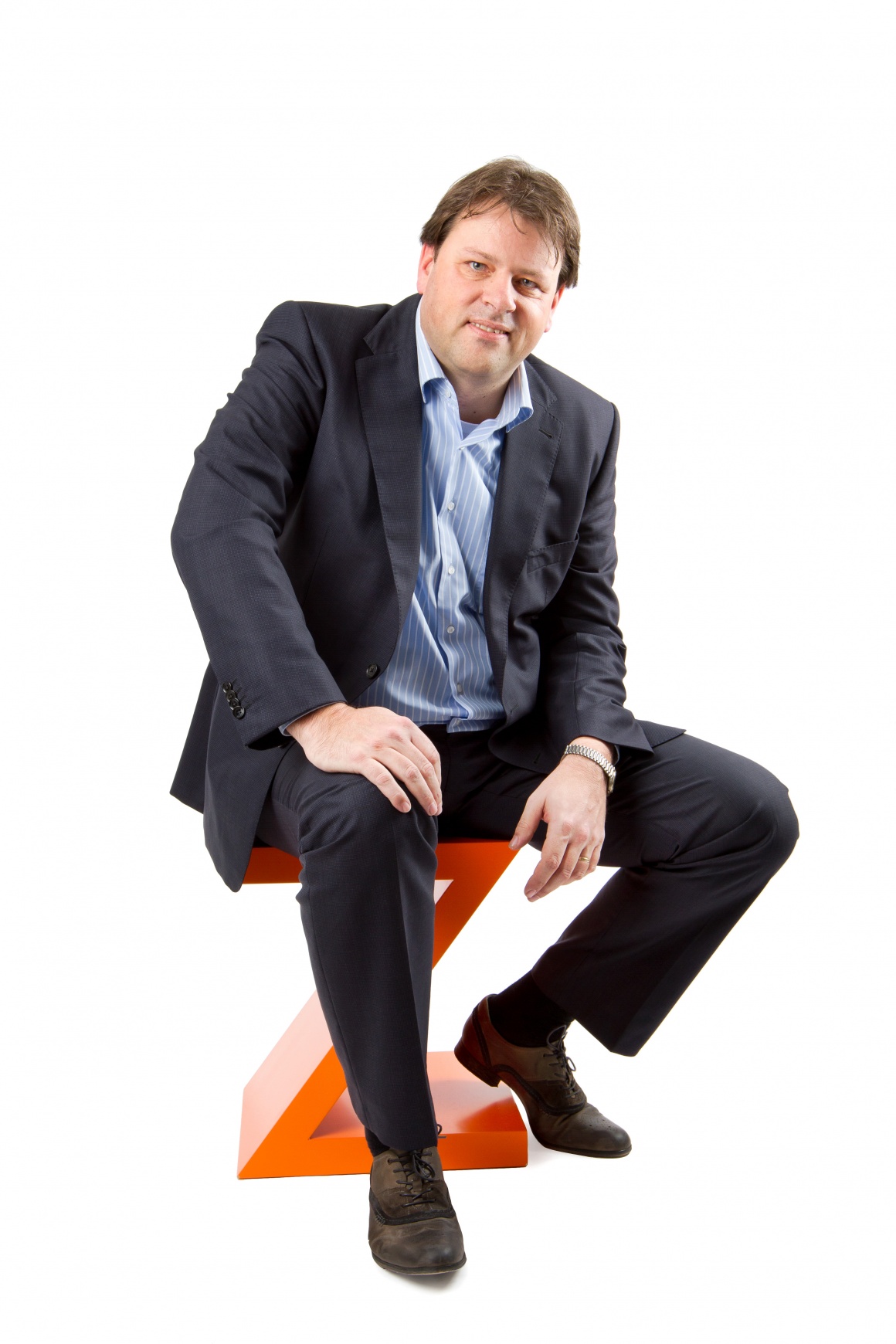
Execute process analysis and business logic
It is always necessary to analyse the order handling and order picking processes to know the advantages that can be achieved.
Key questions to ask are:
- What are the current travel distances of all order pickers, and how many packages per hour do they pick on average?
- Is the product range or part of the range suitable for item-based or order-based multi-order picking, and does that fit within the time windows available for order picking?
For many small, individual orders, it is often not worthwhile to implement multi-order picking due to the expected delivery time, e.g. same-day delivery. However, the order streams of logistics service providers and retailers with more sizeable warehouses and dozens of order pickers are large enough that an investment can usually be recovered within a short timescale. An important consideration to take in this regard is whether the existing ERP and/or WCS/WMS system has the capability to support multi-order picking.
So how does this work in practice?
A.S Watson, Dutch market leader in health & beauty, is a great example of how businesses can benefit from multi-order picking.
Coen Mulder, Functional Control Supply Chain Development at A.S. Watson explains:
“After using single-order picking for a while, with all pickers travelling through the entire warehouse, we got together with Zetes to look at ways to minimise our travel distances. We came to the conclusion that we could achieve about 16% efficiency improvement by combining orders with the support of quantity calculations for taking along the best order carriers (pallets or bins). Based on the business case, we then jointly implemented multi-order picking.”
Jaqueline van Oostrum, Supply Chain and Logistics Project Manager at A.S. Watson adds: “Coupled with minimising travel distances, multi-order picking delivers additional time savings – for example, because staff don’t hinder each other or have to wait in the warehouse alleys. Looking back on this project, we see that our implementation of multi-order picking for the current assortment exceeded everyone’s expectations, with an impressive 38% improvement in efficiency. The average number of packages per hour picked in this order stream has risen from 90 to 125. In light of that success, we have also implemented multi-order picking for part of the special-offer products, with the aim of achieving similar improvements with this second order stream”.